Cutting corners on the maintenance of electrical switchgear or using third party replacement products could end up costing users dearly, as unscheduled repairs and costly breakdowns all have a negative effect on the running of an operation and its profitability. By adopting a preventative approach, it is possible to keep electrical switchgear in better health, identifying potential problems before they cause major disruption and significantly extending the lifecycle of the electrical equipment. Here, Tom Fitzgerald of Schneider Electric shares his 7 steps to preventative maintenance success;
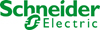
Seven steps for switchgear success
Published: 14 January 2014
Category: News
The old adage that ‘prevention is better than cure’ is never more relevant than when talking about the predictive maintenance of electrical distribution equipment. Simply fixing equipment as it breaks is a high risk strategy, which leaves an operator with no control over the timing or expense of equipment breakdowns. Embracing the idea of preventative maintenance over reactive maintenance can save money and reduce man-hours, which can all have a positive impact on the bottom line.
The concept of preventative maintenance is nothing new, and is something we all do on a regular basis, whether it’s an annual service on your home’s boiler, or a regular service on your car. By closely monitoring the state of these items, we involve experts and technicians who can spot small problems before they become major ones, saving us significant costs in the long term.
Preventative maintenance can take many forms, and at Schneider Electric, we have developed a 7 step strategy for the proactive maintenance of electrical equipment:
Step 1 – Sound installation and commissioning
The successful maintenance of low and medium voltage switchgear starts at the very beginning of the equipment’s life. Proper installation and commissioning is vital to ensure switchgear is able to realise its full potential and sustain high performance levels without premature equipment failure.
Step 2 – Technical training for staff
Once the electrical distribution equipment has been correctly installed, it is important that staff using it, are given the appropriate training in order to maintain the equipment’s long term health. Without proper guidance, equipment can be subject to misuse, which jeopardises the safety of personnel as well as the wellbeing of the switch gear and downstream functions. Technical training should be given when the switchgear is installed, and repeated for new employees or as regular refresher sessions throughout the life of the equipment for existing staff.
Step 3 – Service and maintenance
Routine checks on the equipment are vital to fix, prevent and predict problems in an installation. Medium voltage switchgear should be proactively maintained and serviced by experienced professionals, in the same way as you would have a mechanic service your car at regular intervals to ensure it is kept at its best health. As an initial step, Schneider Electric offers an on-demand maintenance service to periodically check its customers’ switchgear, provide a diagnosis of current issues and offer recommendations for future repairs or replacements.
Step 4 – Upgrading equipment (tested and guaranteed)
When electrical switchgear has been installed for some time, upgrading the equipment can extend its life, without the need for a full replacement of base equipment. Schneider Electric offers ECOFIT™ retrofits – an ecological and economic modernisation concept - as a cost effective means of retrospectively upgrading low and medium voltage equipment. It ensures that installation updates can be done on site and can often be done without a full power down; saving both time and money. ECOFIT™ retrofits can prolong the switchgear’s lifetime by more than 50 per cent, and can optimise service and infrastructure costs by 30 to 70 per cent.
Step 5 – End of life
Once electrical distribution equipment reaches the end of its working life, it is important to dispose of it in a way that is safe for the environment, and compliant with waste regulations. Some companies, like Schneider Electric can process old electrical equipment and recover hazardous substances and pollutants such as SF6 gas and polychlorinated biphenyls (PCBs).
Step 6 – Installation assessment
Before spending money on replacing electrical distribution equipment like for like, it is worth properly assessing the needs of your organisation. Over time, things change and it’s wise to get a site-wide electrical installation assessment – including an evaluation of energy needs, current capabilities and reliability analysis – to help mitigate against risk of failure of key equipment and identify steps to improve the resilience of your electrical distribution network.
Step 7 – Consider outsourcing service for stress-free maintenance
Unexpected downtime can cause significant financial losses, and this can be compounded by repair personnel being slow to respond or equipment that underperforms once it’s been repaired, so it’s worth considering buying in the relevant expertise to ensure low and medium voltage switchgear stays in tip top condition. Agreeing a service support contract with a reputable company can give companies control over their budgets and will guarantee a prompt response in the event of a failure. Before committing to a contract, consider the merits of a longer agreement as this will give improved asset management through the whole spectrum of preventative maintenance. Schneider Electric’s support contracts come in four levels which vary in length and detail depending on the site and installation requirements. Essentially, these contracts act as an insurance policy to protect a business from equipment failure and unexpected repair costs.
When we investigate the lifecycle of equipment through the seven steps, we see that over a long period of time, there are things which can be done to extend the life, reliability and performance of switchgear equipment at every stage. While economic conditions are uncertain, operators can cut costs and improve performance by ensuring their switchgear is given the expert care and attention it needs. You wouldn’t risk your safety by driving a car which has not been regularly checked by a mechanic, and nor should you gamble your business’ productivity by allowing important electrical distribution equipment to underperform or fail. Put your company in the driving seat with preventative maintenance to help your switchgear go the distance.
For further information please visit www.schneider-electric.com/ie.